Research Theme: Power Electronics, Drives and Control (PEDC)
Innovative research of international quality in the area of power electronics systems.
Power Electronics
There is a lot of cross over between the research and researchers within the Power Electronics and Drives & Control subgroups at Newcastle University.
We focus on the development of:
- highly efficient electric drives
- power dense power converters
- intelligent energy management
- advanced controls of power converters
We are also investigating cost-effective silicon carbide and silicon power switching devices. We are using new materials for enhancing cooling power modules.
Our research ranges from power device fabrication through circuits, drives and control to electrical machines. Power Electronics research at Newcastle University forms the largest, most balanced set of expertise in the UK. We are unique in the UK in having significant depth across the sector within a single team.
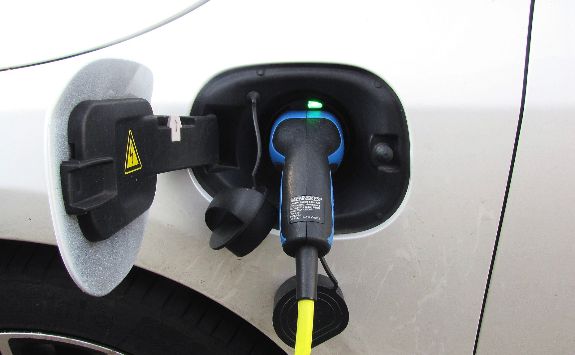
Thermal management
Most failures in power electronics can be attributed to cracks in the solder layer or wire lift-off. Both of these effects are a function of thermal cycling of components. Improved thermal management has the clear potential to improve lifetime.
We are investigating alternative unique cooling management structures for the needs of individual chips.
Contact
New materials
Gallium Nitride converter
In this project, we are examining the practical issues in design, construction and testing of GaN based converter circuits. GaN transistors (FETs) are very fast. Their performance is extremely dependent on parasitic aspects of the circuit layout. To minimise stray inductance, surface mount leadless packages are preferred. But this can result in rapidly changing thermal management when the primary heat flow path is through the PCB.
The high dv/dt associated with GaN transistors also represents a challenge for gate drive circuit design and EMI. We are investigating the use of a cascoded GaN/Si device as a first step in GaN technology. The cascoded GaN MOSFET has a wider safe gate voltage range, so damage due to gate voltage overshoot is less likely
System modelling
The plant emulator is a model of the hardware – converter, motor, and load – which the microcontroller will control. Real-time plant emulation is a useful intermediate step between off-line simulation and full hardware experimental testing.
Conventional simulations include Matlab/Simulink or PLECS. Using this approach allows us to test the controller code in real-time, which conventional simulations are unable to do. The benefits include monitoring precise timing issues. These include issues associated with the interrupt service routines and code execution times.
As the microcontroller is running in real-time, the GUI user interface can be operated in the normal way when in plant emulator mode. We can also view internal variables on an oscilloscope using the DAC outputs on the F28377D.
As well as being a general diagnostic tool, monitoring DAC outputs can be useful for tuning operations. These often prove tedious when carried out on a non-real-time simulator.
Contact
New architectures
Recent developments in voltage source converter technology has shifted the focus from classical two-level configuration into multi-level and modular multi-level converters.
We are pioneering multi-level converters. This includes:
- new topologies
- control and applications for offshore windfarm power transmission at high power DC
- low frequency AC
We are also developing DC/DC converters with the explicit aim of reducing the size and weight of components. We are making these converters from conventional materials. They operate at conventional frequencies.
Contact
Drives and Control
We specialise in the design and implementation of control algorithms for Power Electronics and Electrical Drives.
The main subsystems of electric drives are:
- the power electronic converter
- the electric machine
- the gearbox
- other ancillary parts such as filters
Traditionally, we have treated these as separate entities
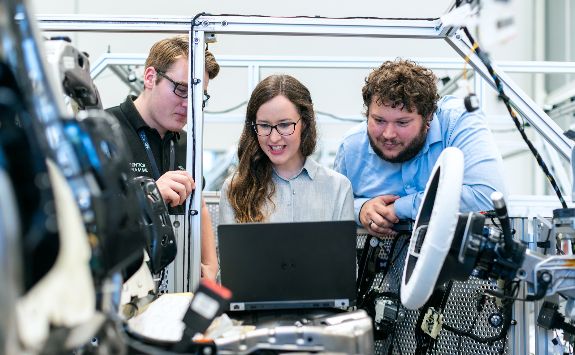
Integrating the electrical components is becoming increasingly important. We need to consider these subsystems in tandem during the design process. We may need to consider them to the point of total functional and mechanical integration.
Integrated systems:
- are smaller
- have greater structural flexibility and enhanced thermal management
- ensure that system integration and modularity are not mutually exclusive
Using Integrated Motor Drives to replace fixed-speed direct on-line motors offers significant advantages. Installation costs are lower and power density is higher compared to discrete motor drive systems.