BioKnit Design Museum
Knitting the future of architecture using fungal mycelium
Published on: 27 November 2023
An arch made from fungal mycelium, grown within 3D knitted fabric formwork, has gone on display at the Design Museum, London.
Challenges and opportunities
A team of researchers from Newcastle and Northumbria universities’ Hub for Biotechnology in the Built Environment (HBBE) are exhibiting their latest BioKnit prototype, a catenary arch that spans over two metres, at the Future Observatory Design Research Exhibition in London.
The arch demonstrates the design possibilities of a biofabrication system that brings together 3D knitted fabric formwork with mycocrete; a unique formulation of mycelium composite, developed by the researchers for use with soft textile moulds.
The BioKnit Arch is a bespoke site-specific structure designed to fit the exact dimensions of the Design Museum gallery.
Dr Jane Scott, NUACT Fellow in the Living Textiles group at the HBBE said: “We were delighted to work closely with the Future Observatory team from the Design Museum in the development of the BioKnit Arch. The exhibition really demonstrates the importance of design research in addressing the challenges and opportunities of the Green Transition
“There are significant challenges in working with such precision using new biohybrid materials, however the accuracy is achieved through a process that integrates parametric modelling, biotechnology and digital fabrication of knitted modules.”
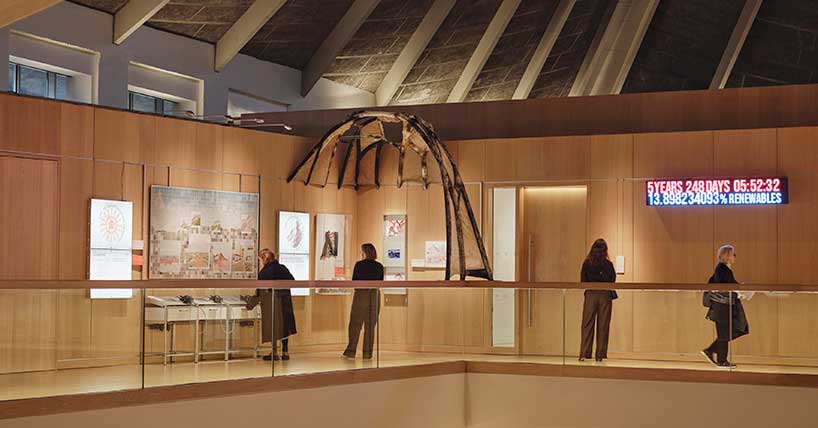
Future Observatory
To make BioKnit prototypes using fungal mycelium, the research team mix mycelium spores with water and cellulose rich substrate materials including sawdust and paper fibres. This forms a viscous paste that is injected into tubular sections of the knitted fabrics. The environmental conditions are controlled to ensure a dark, warm and humid environment to allow the mycelium to grow. To generate the extraordinary 3D form, the structure is suspended, and as the mycelium grows, binding the substrates together, it transforms the soft flexible knitted textile into a rigid biocomposite.
Growing as construction presents an opportunity to rethink a lot of the conventional construction processes and to develop new sustainable practices. Biofabrication has the flexibility to work locally either on site or off site, to reduce transportation associated with shipping individual parts for assembly. The team have also begun to work with local waste substrates to produce mycocrete with the aim of developing carbon negative materials for use in construction.
The research proposes applications for BioKnit in non-load bearing applications in buildings, for internal linings and to shape space. The ability to produce new geometries, curved surfaces and organic forms is very compelling for future architecture as well as new aesthetics and new tactile experiences that emerge from mycelium coming together with textiles at an architectural scale.
Dr Scott added: “There are significant challenges in working with such precision using new biohybrid materials, however the accuracy is achieved through a process that integrates parametric modelling, biotechnology and digital fabrication of knitted modules.”
The BioKnit arch is one of six items on display in the new exhibtion which showcases six researchers from across the UK who are confronting environmental concerns and working towards liveable futures.
The Future Observatory display space is dedicated to ongoing, forward-facing research projects. The initiative signals the importance of placing design at the heart of the green transition, for both the museum and the broader design industry.
The exhibitors are: Faber Futures, CLIMAVORE, Julia King, Hub for Biotechnology in the Built Environment, Dunne & Raby and Dark Matter Labs.