Research Group: Fluid Dynamics and Thermal Systems
Internationally renowned research in Combustion, Fluid Dynamics, Fuel Cell, Heat and Mass Transfer, Multi-phase flows.
Our group carries out a wide range of research work. Our research activities span the broad area of Thermofluid dynamics.
Flows occurring in nature or engineering applications are frequently turbulent. As a group, we are involved in mathematical, experimental and numerical investigations of turbulent reacting (e.g. combusting flows) and non-reacting flows. We utilise the advancements of high-performance computing to carry out high-fidelity simulations of turbulent reacting and non-reacting flows involving both single phase and multi-phase fluids.
From this, we develop models for engineering applications. Our models lead to greener and more efficient power generation devices. We also investigate turbulent boundary-layer flows and wall-turbulence. We have developed super-miniature sensors for turbulence measurements. We are developing innovative skin-friction drag reduction and flow-separation control technologies.
Our research into heat and fluid flow also involves heat and mass transfer in nanofluids and non-Newtonian fluids.and transport processes in fuel cells and Li-ion batteries.
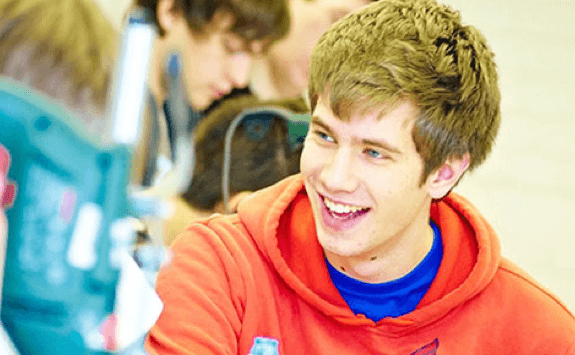
Computational research
We develop in-house CFD (computational fluid dynamics) code and algorithms. We use open-source industrial code. We are experts in the use of common software packages. We combine these areas of expertise for fundamental physical investigation of industrial problems.
We carry out advanced simulations of turbulence and heat transfer. We investigate turbulent reacting flows, multiphase flows and complex non-Newtonian fluids.
We undertake physics-based modelling of fuel cells and Li-ion batteries. Our investigations extend to related electrochemical energy devices. We use multi-scale computational modelling to study fuel-cell stacks and battery packs.
Our research also focuses on health. We undertake computational modelling of blood flow in arteries.
Experimental research
We undertake applied thermodynamic investigations in energy generation, storage and refrigeration. We explore water and thermal management in polymer electrolyte fuel cells
We are developing tuneable porous media for clean energy applications. This includes microstructural characterisation.
We are carrying out electro-thermal characterisation of Li-ion batteries. We are improving their recycling and re-use. We are using infrared (IR) thermography to detect defects in a range of devices. We carry out thermal design and optimisation inspired by nature.
We are investigating convective heat transfer of Newtonian and non-Newtonian nanofluids. Our experiments include turbulent drag reduction, turbulent boundary-layer flows and flow separation control.
We develop micro-sensing and micro-actuation technologies.
Development of high-fidelity Computational Fluid Dynamics (CFD) methodologies
Our research in this area includes:
- developing new algorithms for numerical modelling fluid flow problems
- developing new software for solving fluid flow problems on high performance computing platforms
- using CFD software for flow prediction in industrial problems
Direct Numerical Simulations (DNS) of turbulence, combustion, heat transfer and multi-phase flows
Our research is leading to a deeper understanding of turbulence and combustion.
We develop mathematical models from Direct Numerical Simulation data.
We investigate turbulent mixing phenomena. We explore turbulent combustion in all its guises: premixed, non-premixed, partially-premixed and stratified. We examine droplet-laden chemically reacting flows.
Modelling of turbulent flows involving combustion, mixing and heat transfer
We utilise the advancements in high-performance computing to conduct Direct Numerical Simulations (DNS) of single/multi-phase turbulent flows with and without chemical reactions (e.g. combustion) and heat transfer without any physical approximations by resolving all the physically relevant length and time scales of turbulence. The physical insights gained from these high-fidelity simulations are in turn utilised to develop models to aid the design process of energy-efficient and environmentally friendly devices for power generation and propulsion sectors. Our research campaign also includes simulation of modelling of combustion processes of high hydrogen content fuels and sustainable biofuels.
Numerical modelling of natural convection of complex non-Newtonian fluids
The viscosity of non-Newtonian fluids changes with movement or force. For example, ketchup is a non-Newtonian fluid as it becomes thinner when you shake it. Nanofluids are fluids containing nanoparticles. The viscosity of shear-thickening liquids increases with stress and decreases in shear-thinning fluids. We investigate the natural and mixed convection of inelastic and yield stress fluids. Process industries, solar power applications and electronic cooling applications use such fluids.
Modelling and simulation of Polymer-Electrolyte Fuel Cells (PEMFCs)
Our research is improving the fundamental understanding of thermal transport and degradation.
We have advanced expertise in the use of COMSOL. We use the software to carry out physics-based modelling and simulation of lithium-ion cells.
We are developing a reduced-order model for battery packs. We are investigating second life behaviour of lithium-ion batteries. We are carrying out parametric studies and performance optimisation.
Physics-based modelling of lithium-ion batteries
Our research is improving the fundamental understanding of thermal transport and degradation.
We have advanced expertise in the use of COMSOL. We use the software to carry out physics-based modelling and simulation of lithium-ion cells.
We are developing a reduced-order model for battery packs. We are investigating second life behaviour of lithium-ion batteries. We are carrying out parametric studies and performance optimisation.
Defects detection using infrared (IR) thermography
An ever-increasing number of applications use electrochemical energy devices. This is because they are both efficient and environmentally friendly. We combine experimental and numerical approaches to detect defects in these devices.
We design non-destructive experiments and develop diagnostic tools and sensors. We identify detection criteria. We provide guidance on scaling up for manufacturing.
Nature inspired thermal design and optimisation using nanofluids
We develop thermal design for electronic cooling and solar thermal applications. We use nature as an inspiration for designing elements such as fins and flow channels. We base our designs on pseudo-fractal structures such as tree branches, leaf veins, watersheds and bronchial tubes.
These designs provide better heat transfer and higher thermal performance. This is beneficial for the industry. It provides improvements for applications including electronic cooling, solar thermal, and heat exchangers.
We investigate convective heat transfer and entropy generation of nanofluids in cavities. Our investigations use theoretical and computational modelling.
Recycling and reuse of li-ion batteries
We carry out electro-thermal characterisation of electric vehicle (EV) batteries. This characterisation allows us to develop testing methods. Our methods optimise the reuse, resource recovery and safety of batteries.
We undertake chemical characterisation of used cells. Our research includes optimum pack and cell design for end of life reuse and recycling.
Industrial and academic links
Within the University, we have strong links with various research groups, including:
The group collaborates with internationally renowned colleagues from many leading international organisations.
Professor Nilanjan Chakraborty was the co-organiser of a workshop on high-pressure combustion. ERFOTAC has funded the workshop. He is also the editor-in-chief of a special issue of Combustion Science and Technology. The special issue was devoted to computational analysis of turbulent reacting flows.
He is also the co-leader of the Sprays and Droplets, Combustion Science and Technology Special Interest Groups (SIGs). These groups belong to the UK-Fluids Network. Prof. Chakraborty is the PI and chair of the UK Consortium on Turbulent Reacting Flows (UKCTRF) and also a member of the steering committees of the Computational Science Centre for Research Communities (CoSeC), and UKRI’s Exascale Computing Algorithms and Infrastructures Benefiting UK Research (ExCALIBUR). He is also a member of EPSRC’s e-infrastructure Strategic Advisory Team (SAT).
Dr Prodip Das is part of one of the Faraday Institution’s flagship projects: Recycling of Li-Ion Batteries (ReLiB).
Dr Richard Whalley is involved in a NATO AVT-254 plasma flow control project. in the new NATO AVT-344 group on Microtechnologies for Air and Space Propulsion.
Several group members belong to a variety of SIGs in the UK-Fluids Network. Topics include combustion science and technology, non-equilibrium turbulence, sprays and droplets, turbulent drag reduction.
A global collaborative network
We also have active collaboration with industries and academic institutes. For example, our global collaborative network stretches from North America to Australia.
UK and Europe
- Cambridge University Engineering Department, UK
- Imperial College London, UK
- University of Liverpool, UK
- University of Birmingham, UK
- Universität der Bundeswehr München, Germany
- Chalmers University, Sweden
- University of Duisburg, Germany
- University of Zaragoza, Spain
North America
- Lawrence Berkeley National Laboratory, USA
- Sandia National Laboratory, USA
- University of Waterloo, Canada
- University of Wisconsin-Madison, USA
Asia
- King Abdullah University of Science & Technology, Saudi Arabia
- Kyoto University, Japan
- UM-SJTU joint institute, Shanghai Jiaotong University, China
- Tianjin University, China
- Bangladesh University of Engineering of Technology, Bangladesh
Australia
- University of New South Wales, Australia
Esteem indicators
We have taken part in many professional activities, both nationally and internationally. These include activities such as journal editorships and conference chairs.
Five recent papers by our group members have been chosen as Editor’s pick by Physics of Fluids. The authors are Dr Umair Ahmed, Dr Prodip Das, and Prof Nilanjan Chakraborty. One of the papers, co-authored by Prof Chakraborty, was used as a cover page material for the January 2019 issue of the Journal of Fluid Mechanics. Dr. Das’s recent research on convective heat transfer and Nanofluids featuredin the Science Highlight (Scilight), which showcases the most interesting research across the physical sciences published in AIP Publishing Journals.
- member of the Royal Society International Exchanges Panel
- Fellow of the Combustion Institute (2021-)
- PI and chair of one of the EPSRC funded High-End Computing consortia: the UK Consortium on Turbulent Reacting Flows (UKCTRF)
- steering group member of the Computational Science Centre for Research Communities (CoSeC)
- editor of the Engineering and Material Science chapter for the science case for Exascale computing commissioned by EPSRC
- steering group member of the UKRI’s Exascale Computing Algorithms and Infrastructures Benefiting UK Research (ExCALIBUR) Steering Committee
- co-edited a special issue on high pressure turbulent premixed combustion for the journal Combustion Science and Technology
- co-edited a special issue on numerical modelling of reacting and non-reacting multi-phase flows for the journal Fluid
- many invited talks in universities and conferences, including, Shanghai Jiao Tong University (China) and Duisburg University (Germany)
- editorial board member of ISRN Journal of Mechanical Engineering, Fluids, and American Journal of Engineering and Applied Sciences
- Guest editor of a special issue of Energies
- founding Associate Editor of the journal Energy 4.0, Elsevier, Netherlands
- editorial board member of three journals: Energies, Sustainability, and Inventions
- Advisory Board Member of the journal Challenges
- organised and chaired many conference tracks, sessions and symposiums, including the Fuel Cell Science, Engineering and Technology Conference, and the ASME International Mechanical Engineering Congress & Exposition
- organising committee member of the World Fuel Cell Conference and the International Conference on Mechanical, Automotive and Materials Engineering
- invited to contribute a book chapter on Heat and Fluid Flow in Porous Media for Polymer-Electrolyte Fuel Cells, in Convective Heat Transfer in Porous Media, CRC Press, USA
- invited talks in universities and conferences, including, but not limited to, Shahjalal University of Science and Technology (Bangladesh) and Simon Fraser University (Canada)
- external reviewer for the Advanced Light Source (ALS) Tomography Science Program, Lawrence Berkeley National Laboratory, USA
Dr Immanuvel Paul
- Invited to contribute a book chapter on Immersed Boundary Methods, Springer
- Invited talks in universities including at Stanford University, USA and Indian Institute of Technology Bombay, India.
- Organising committee member for various workshops and conferences in the UK and the US.
- invited international speaker at the US Air Force’s annual program review in Washington DC
- work package leader for the NATO AVT-254 plasma flow control project
Funding and computing support
- EPSRC
- Nuffield Foundation
- Department for Transport
- United States Air Force: Air Force Office of Scientific Research
- The Royal Society
- Japan Society for the Promotion of Science
- Archer
- UK Consortium on Turbulent Reacting Flows
- DFG: Deutsche Forschungsgemeinschaft
- Airbus
- British Council
- Royal Academy of Engineering
- Science & Technology Facilities Council
- The Faraday Institution
- Aerospace Technology Institute
- UK Turbulence Consortium
Current projects
We are keen to hear from prospective PhD students and Postdoctoral Research Associates. Contact the academic staff member whose research interests match your own to discuss things further.
Current research interests in the Group include:
- simulation and modelling of turbulent reacting flows
- theoretical, computational and experimental analysis of disperse multiphase turbulent flows
- quantum turbulence
- heat and mass transfer in solid-liquid phase change applications
- heat transfer involving non-Newtonian fluids
The following list is not exhaustive and other projects may be available.
Dr Richard Whalley
Coherent structures, mixing efficiency in a turbulent starting jet with and without strong swirling component
We will conduct data analyses on the existing PIV experimental data. Both statistical independent and temporal resolved stereo PIV data are available.
We will investigate physical interpretations of coherent structures and turbulent/non-turbulent interface behaviours. We will use various mathematical tools, including:
- Proper Orthogonal Decomposition (POD)
- Dynamic Mode Decomposition (DMD)
- wavelet analyses
- Contact Dr Richard Whalley
Evolution of near field turbulence generated by mono-plane multi-scaled grids
We will analyse existing PIV experimental data of near field turbulence. The turbulence has been generated by a mono-planed multi-scaled grid. Both statistical independent and temporal resolved data are available.
We will compare statistics and time responses of physical quantitates among the flow fields generated by three types of grid.
- Contact Dr Richard Whalley
Experimental study of multi-phase turbulent boundary layer flows
This project will investigate the interaction of the coherent structures in a turbulent boundary layer and the second phase inertial particles.
We will carry out experiments in the existing water channel. We will use 2D, stereo and the in-house developed tomo PIV or stereo-scanning PIV. We will use the results to support the PDF (Probability Density Function) modellings in such flows.
- Contact Dr Richard Whalley
Experimental technique development and improvement on the in-house tomo PIV code
This project will improve the existing in-house tomographic PIV code. The code is in MatLab and FORTRAN.
We will add more features. We will add subroutines, such as multi-phase flow compatible. We will improve the structure of the existing working code to advance the performance (computation speed and accuracy). We will test the code in experiments, for example in a two-phase vortex ring or two-phase boundary layer flow.
- Contact Dr Richard Whalley
From radioactive particles to underwater light climates: turbulent boundary layer multiphase flows
Most flows in nature or in technological applications are turbulent. Many turbulent flows are inter-dispersed with particles which alter the dynamics of the fluid flow.
In this project, we will use advanced experimental laser-based flow measurement techniques. These will include scanning stereoscopic particle image velocimetry. We will also use advanced mathematical modelling and computational simulations. Combined, these will allow us to explore how inertial particles alter the structure of the turbulent boundary layer.
We will develop a deeper physical understanding of these multiphase flows. This may allow us to predict the kinematics and dynamics of radioactive particles released into the atmosphere. It will provide a better understanding of the pneumatic transport of particulates in pipes. It will allow us to optimise the design and performance of particle separation systems. We will gain insights into the deposition and transport of sedimentation on our sea beds.
- Contact Dr Richard Whalley
Hibernating turbulence: towards developing the next generation of drag reduction devices
The most successful turbulence control technique is the dissolution of rheology-modifying additives to the working fluid. But it can only be used in liquid flows. Additives can reduce turbulent energy consumption by as much as 80%. This yields an effect known as Maximum-Drag-Reduction (MDR).
Recent cutting-edge, scientific research has found that MDR is closely linked to a low-drag state known as “hibernating turbulence.” We will use a high-molecular-weight polymer to reduce the skin-friction drag of a turbulent boundary layer to the MDR regime. By doing this, we will study the hibernating turbulence phenomena. A deeper physical understanding of hibernating turbulence may lead us to obtaining MDR in gas flows. This has the potential to transform the aerospace industry.
- Contact Dr Richard Whalley
Mixing at the micro-scale: creating turbulence in micro-flows
Mixing at the micro-scale is notoriously difficult. The creeping flow of a viscous fluid through sub-millimetre channels is laminar. It is steady with a Reynolds number often smaller than 1. Thus, efficient mixing and heat transfer to the fluid is slow. This is because these processes are dominated by diffusion and conduction.
In this research, we will investigate novel micro-mixing technologies. We will create turbulence-like motions within micro-channels to ensure rapid fluid mixing and enhanced heat transfer. This will lead to the development of the next-generation of lab-on-a-chip devices.
- Contact Dr Richard Whalley
Pumping with no moving parts: innovative low-voltage micro-pumps
The integration of several components onto a silicon chip has long been a goal of micro-fluidics designers.
Development of Micro-Electro-Mechanical Systems (MEMS) is ongoing. Such developments mean that we inch ever closer to the possibility of generating a lab-on-a-chip device. On many miniature devices, the transportation, mixing or control of fluid needs a micro-pump. Devices need micro-pumps for a variety of reasons, including:
- movement of coolant through a micro heat exchanger
- delivery of a millilitre-size dose of insulin to a diabetic patient
- the transfer of biological samples through Micro Total Analysis Systems (µTAS)
In this experimental investigation, we will design, develop and test innovative low-voltage micro-pumps. We will use a state-of-the-art micro-particle image velocimetry system.
- Contact Dr Richard Whalley
Mixing at the micro-scale: creating turbulence in micro-flows
Over 50% of the total drag of a commercial aircraft is due to turbulent skin-friction drag. Reducing this friction would lead to vast economic savings. It would also provide wider health and environmental benefits through improved air quality.
We will design innovative surface plasma actuator arrays. These will reduce the skin-friction drag of wall-bounded turbulent flows. We will measure the changes in turbulent boundary-layer structures. To do this, we will use state-of-the-art laser-based flow measurement techniques such as laser Doppler velocimetry and particle image velocimetry. We will monitor the reductions in drag with thermal anemometry.
- Contact Dr Richard Whalley
Turbulent vortex rings/puffs from various initial conditions and confinements
Initial conditions and ambient confinements have an effect on the formation and long term evolution of high Reynolds number turbulent vortex rings and/or turbulent puffs. Initial conditions include nozzle shapes and controlled perturbations. Ambient confinements are found in, for example, cylindrical tubes.
We will design different initial and confinement conditions. We will then conduct experiments in the large vortex ring generator. We are able to achieve good spatial and temporal resolution with the existing high speed, high resolution cameras and a PIV system.
- Contact Dr Richard Whalley
Vortex dynamics within the cardiac left ventricle of the heart
Vortex rings are of fundamental importance across many branches of fluid mechanics. They have been observed in viscous starting jets, volcanic eruptions, jet propulsion, and in many biological flows.
We will study the vortex dynamics associated with the left ventricle of the heart. To do this, we will use a synthesised blood-like fluid. We will investigate the vortices with stereoscopic particle image velocimetry. This is a state-of-the-art laser-based flow measurement technique.
The research will provide a deeper understanding of the kinematics and dynamics of these vortical flow structures. This may play a crucial role in detecting cardiac dysfunction. It may also contribute to the development of future healthcare technologies.
- Contact Dr Richard Whalley
Prof Nilanjan Chakraborty
Nilanjan Chakraborty is Professor of Fluid Dynamics. He joined Newcastle University in 2011. He leads the Fluid Dynamics and Thermal Systems research group. He has previously worked for the University of Liverpool, Cambridge University, and General Electric in India.
Nilanjan’s research focuses on modelling turbulent premixed/stratified flames and localised ignition of turbulent gaseous and droplet-laden inhomogeneous mixtures. His research interests include:
- Direct Numerical Simulation (DNS) of turbulent combustion
- Large Eddy Simulation (LES) and Reynolds Averaged Navier Stokes Simulation (RANS) combustion modelling
- natural convection and mixed convection of Newtonian and non-Newtonian fluids
- melting/solidification related heat transfer problems in classical manufacturing and laser aided manufacturing applications
- numerical modelling of multi-phase flow
- high performance computing
- Computational Fluid Dynamics (CFD)
- Google Scholar
Fundamental understanding and modelling of turbulent coal particle laden mixtures using Direct Numerical Simulations
Multi-phase turbulent reacting flows play a key role in several important engineering processes. These include:
- coal combustion for power generation
- droplet combustion in Internal Combustion (IC) engines and gas turbines
This has major implications for the grand challenges faced by modern societies. It has a major effect on energy efficiency and environmental friendliness.
Several engineering applications are in seminal areas. But much of the existing research in multi-phase reacting flow applications is based on experimental observation. It often relies heavily on empirical relations.
This project will address the gasification and combustion process for coal. We will use Direct Numerical Simulations (DNS). DNS allows investigation of the physical processes associated with turbulent flow without major physical approximation. Such simulations are either rare or non-existent in the open literature.
DNS simulations will provide us with fundamental physical understanding. We will then develop more accurate combustion models for Large Eddy Simulations (LES) and Reynolds Averaged Navier Stokes (RANS) simulations of pulverised coal particle laden combustion. We will devise new models based on analysis of DNS data – i.e. a priori analysis. This will give rise to high fidelity computational tools for designing new generation combustors. These combustors will be efficient and environmentally friendly.
The research will be of interest to those involved with designing new generation boilers and combustors. We will keep interested industrial parties informed during the course of this project. We will invite them to attend the progress review meetings. We will also publish project outcomes in reputed journals (e.g. Combustion and Flame, Physics of Fluids, Proceedings of the Combustion Institute) and conference proceedings (e.g. International Symposium on Combustion, European Combustion Meeting).
This work is fundamental. We expect that internationally reputed journals will publish project outcomes. The student will work with combustion groups at the University of Cambridge. There is also scope to interact with reputed combustion researchers in the USA, France and Germany.
You will be eligible for this project if you:
- have a 1st class or 2:1 degree in Aerospace, Mechanical and Chemical Engineering, Applied Mathematics, or Applied Physics
- are interested in general area of turbulent combustion
- Contact Prof Nilanjan Chakraborty
Fundamental understanding and modelling of turbulent stratified mixture combustion using Direct Numerical Simulations
In several engineering applications, combustion takes place in a configuration between the fully premixed and fully non-premixed regime. This is often referred to as stratified charge combustion or partially premixed combustion.
Recent pollution control regulations call for an environmentally friendly combustion process. To achieve this in Compression Ignition (CI) engines, some mixing between fuel and air needs to take place before the combustion process. These new generation CI engines are called Homogeneous Charged Compression Ignition (HCCI) engines.
There are many numerical studies on either premixed or non-premixed combustion from a variety of viewpoints. The amount of modelling information available for stratified charge combustion is relatively scarce.
In this project, we will carry out Direct Numerical Simulations (DNS) of stratified charge combustion. We will resolve all the relevant length scales and timescales of turbulent reacting flow without any kind of turbulence modelling. The DNS data can be treated as experimental data with infinite resolution.
As a first step, we will use three-dimensional (3D) DNS with simplified chemistry. This will provide a fundamental understanding of the thermal aspect of the stratified charge combustion process. Based on this understanding, we will carry out detailed chemistry-based 3D simulations. We will then use the data to develop Computational Fluid Dynamics (CFD) models for addressing turbulent stratified charge combustion.
This work is fundamental. We expect that internationally reputed journals (eg Combustion and Flame, Physics of Fluids, Proceedings of the Combustion Institute) and conference proceedings (eg International Symposium on Combustion, European Combustion Meeting) will publish project outcomes. The student will work with combustion groups at the University of Cambridge and reputed combustion researchers in the USA, France and Germany.
You will be eligible for this project if you:
- have a good background in Mathematics, Fluid Mechanics and Thermodynamics
- have some experience of computer programming
- Contact Prof Nilanjan Chakraborty
Modelling non-unity Lewis number effects on turbulent scalar flux transport in premixed turbulent combustion in the context of Large Eddy Simulations
Turbulent scalar flux modelling plays an important role in computational modelling of turbulent reacting flows. The usual modelling practice uses gradient hypothesis. But it does not capture the behaviours of turbulent scalar flux under some conditions. These behaviours are both quantitative and qualitative. This is in the context of Reynolds Averaged Navier Stokes (RANS) and Large Eddy Simulations (LES).
The relative strength of thermal diffusion to mass diffusion has important effects on turbulent scalar transport in turbulent premixed flames. It is characterised by a non-dimensional number known as the Lewis number. This number is the ratio of thermal diffusivity to mass diffusivity. Flames with a Lewis number much smaller than unity show counter-gradient scalar transport. The scalar transport is gradient type for flames with a Lewis number close to unity. Both are under identical initial turbulent flow conditions. The modelling of Lewis number effects on scalar flux transport in the context of RANS has been addressed before. It has not yet been modelled in the context of LES.
In this project, we will use explicit LES filtering of Direct Numerical Simulation (DNS) data of turbulent premixed flames. This will enable us to carry out a priori modelling of turbulent scalar fluxes in the context of LES. We will then use the developed model to carry out LES simulations of turbulent premixed combustion.
The UK Government has set legally binding targets for emissions reductions. These require a reduction in emissions of 57% from 1990 to 2030. Hydrogen is a major alternative fuel to limit greenhouse gas emissions in the future. But most Internal Combustion (IC) engines and gas turbines operate using hydrocarbon fuels.
The chemistry and transport properties of hydrogen are significantly different from those of most hydrocarbons. Switching from conventional hydrocarbon fuels to hydrogen is likely to take place gradually. In the interim phase, hydrogen will be blended with standard hydrocarbon fuels. Hydrogen in hydrocarbon-air mixtures introduces significant differential diffusion between heat and species. Thus, the findings from this project will be beneficial for modelling the turbulent transport in hydrogen blended in premixed turbulent hydrocarbon flames.
This work is fundamental. We expect that internationally reputed journals will publish project outcomes. The student will have ample opportunity to work with combustion groups at the University of Cambridge as well as reputed combustion researchers in the USA, France and Germany.
You will be eligible for this project if you:
- have a 1st class or 2:1 degree in Aerospace, Mechanical and Chemical Engineering, Applied Mathematics, or Applied Physics
- are interested in the general area of turbulent combustion
- Contact Prof Nilanjan Chakraborty
Numerical modelling of natural convection of Bingham fluids in rectangular enclosures for different inclinations with vertical direction
Natural convection in enclosed spaces has several applications, including:
- electronic cooling
- solar collectors
- heating and preservation of food
There is an extensive analysis of natural convection of non-Newtonian fluids in rectangular enclosures. But there has been comparatively little effort directed to the heat transfer of yield stress fluids.
This project will analyse the natural convection of non-Newtonian yield stress fluids in rectangular enclosures. We will use numerical simulations.
Bingham fluid is a special type of yield stress fluid. It exhibits a linear strain rate dependence of shear stress. We will carry out detailed analyses of the effects of:
- the Bingham number
- the Rayleigh number
- the aspect ratio
- the inclination with the vertical direction
We will carry out these analyses for both laminar and turbulent conditions. The Nusselt number is the ratio of convective to conductive heat transfer across a boundary. Using the simulation data, we will calculate the correlations for the mean Nusselt number as a function of nominal Rayleigh, Prandtl and Bingham numbers, as well as the angle with the vertical direction.
This work is fundamental. We expect that internationally reputed journals will publish project outcomes (eg International Journal of Heat and Mass Transfer, Numerical Heat Transfer) and conference proceedings (eg International Symposium on Advances in Computational Heat Transfer). The student will have ample opportunity to work with collaborators and experts in this field of study.
You will be eligible for this project if you:
- have a good background in Mathematics, Fluid Mechanics and Thermodynamics
- have some experience of computer programming
- Contact Prof Nilanjan Chakraborty
Numerical modelling of turbulent transport in laser welding of dissimilar metal couple
Laser aided materials processing takes a key role in most modern methods of manufacturing. Laser welding is one of the most common laser aided materials processing operations.
The mechanical strength and microstructure of the welded joint strongly depend on the thermal histories in the fusion zone and the nearby unmelted region.
Molten metal flow has a considerable effect on thermal histories and solidification processes. Predicting the thermal behaviour of the process requires a thorough knowledge of the transport mechanisms inside the laser molten pool. These mechanisms lead to a final resolidified microstructure. We can use this knowledge in determining process parameters to provide a welded joint of the required quality. The parameters include welding power and laser beam-scanning speed.
We will study the heat, momentum and species transport in laser molten pool in detail. We will base our studies on Computational Fluid Dynamics (CFD) simulations. Under most practical operating conditions, the molten pool convection is turbulent in nature. But modelling turbulent transport in molten metal pools in dissimilar metal welding is not yet done. Dissimilar metal welding is inherently three-dimensional (3D) in nature. Thus, we will carry out 3D unsteady Detached Eddy Simulations (DES) simulations.
We want to keep the study simple at the same time as having a fundamental physical insight. To achieve this, we will investigate a dissimilar couple based on copper (Cu) and Nickel (Ni). Cu and Ni are completely miscible in both liquid and solid phases, but have very different physical properties. Based on fundamental understanding, we will carry out a systematic parametric study. This study will examine the effects of process parameters on key features of the molten pool, including:
- maximum temperature
- pool penetration
- pool aspect ratio (ratio of width to depth).
We will disseminate the project outcome through journal articles and conference proceedings.
This work is fundamental. We expect that internationally reputed journals will publish project outcomes (eg International Journal of Heat and Mass Transfer, Numerical Heat Transfer) and conference proceedings (eg International Symposium on Advances in Computational Heat Transfer). The student will have ample opportunity to work with collaborators and experts in this field of study.
You will be eligible for this project if you:
- have a good background in Mathematics, Fluid Mechanics and Thermodynamics
- have some experience of computer programming
- Contact Prof Nilanjan Chakraborty
Phase-space numerical methods for studying particle transport in turbulent boundary layers
Laser aided materials processing takes a key role in most modern methods of manufacturing. Laser welding is one of the most common laser aided materials processing operations.
The transport of particulates in fluid flow is of central concern to many industrial processes. For example, effective pre-mixing of fuel particles within a gas flow is crucial to the efficiency of the combustion process. It can also have a significant effect on the physical and chemical characteristics of resulting combustion products, and the ease with which they can be filtered.
In multi-phase flows, the gas flow is predominantly turbulent. Modelling and computational difficulties arise in single-phase turbulence. The presence of the particulate phase further compounds these difficulties. Fundamental modelling issues in the study of such multi-phase flow systems include:
- the treatment of particle-particle and particle-surface interactions
- turbulence attenuation by particulate material (two-way coupling)
Particle-surface interactions are often a primary influence on overall transport. They are the focus of the work we propose, which concerns the application of probability density function (PDF) models. These models describe the statistical distribution of particles in an extended phase-space framework. They allow for the accurate treatment of particle-surface interactions. We will develop equally accurate and efficient numerical schemes. These will be capable of treating the increased dimensionality of these phase-space models.
Previous work identified an elegant reduction of dimensionality leading to a system of coupled Fokker–Planck type equations. These describe the transport of phase-space conditioned moments of particle and fluid velocities, both stream-wise and wall-normal. This system is unlike conventional moment-based transport equations. It allows for exact treatment of particle deposition at the flow boundary. It also provides an efficient way to handle a 5-dimensional phase-space domain. Moreover, the equations in the system are linear, so we can solve them in a sequential fashion. There is no closure problem to address. A hybrid Hermite/Discontinuous Galerkin scheme has been developed to treat this system. Hermite basis functions in combination with an iterative scaling approach offer the potential for accurate, efficient computation of solutions.
This project will involve the further development and application of the modelling and numerical approach. We will consider both particle deposition and elastic particle-surface collisions. We will develop the PDF numerics. We will also design hybrid models/numerics that allow the coupling of PDF models to more conventional two-fluid type models. This is more appropriate for transport in the bulk flow.
You will be eligible for this project if you:
- have a minimum 2:1 degree in Applied Mathematics, Physics, or a relevant Engineering discipline
- have a good knowledge of basic fluid dynamics
- have some knowledge of turbulence modelling methods
- some background in the study of computational methods, ideally in the context of fluid flow problems
- Contact Prof Nilanjan Chakraborty
Understanding and modelling of turbulent premixed flame-wall interaction using Direct Numerical Simulations
There are many studies on all bounded turbulent flows under isothermal conditions. But these studies are principally from the point of view of drag reduction. There has been relatively limited analysis of the turbulent boundary layer in reacting flows.
Gases expand due to heat release, often caused by a chemical reaction. This has a significant effect on the velocity and heat transfer pattern within a turbulent reacting flow boundary layer. These can be very different from those obtained in turbulent isothermal wall bounded flows. Understanding this behaviour is pivotal for designing efficient Spark Ignition (SI) engines and industrial gas turbine combustors. In turbulent premixed flames, reactants are mixed before combustion. These elements quench when they approach the cylinder walls.
This flame quenching leads to unburned hydrocarbon fuel. The associated heat transfer to the cylinder wall leads to heat loss from the cylinder. Both of these act to reduce the efficiency of SI engines. Thus, a thorough understanding of flame-wall interaction is essential for designing a new generation of internal combustion engines.
In-cylinder conditions are hostile, so we can’t take reliable measurements by experimental means. Numerical simulations often use Reynolds Averaged Navier Stokes (RANS) and Large Eddy Simulations (LES). Physical processes may be associated with length scales smaller than computational grid spacing. RANS and LES use turbulence models to approximate these processes.
Reliable data for flame-wall interaction is often unavailable. This compromises the predictive capability of these models. Boundary layers involving turbulent reacting flows are often modelled using isothermal flow conditions. But this modelling is inaccurate.
Increased computer power offers an important research avenue to investigate the effect by providing the means for Direct Numerical Simulations (DNS). In DNS, all the relevant turbulent length and time scales are adequately resolved. But DNS is expensive and impractical for all complex geometries of engineering interest. This project considers DNS of turbulent premixed flame-wall interaction in a simple configuration. We will develop an adaptive grid refinement based on the position of the flame. Both the chemical structure with the flame thickness and the coherent structures within the wall boundary layer need to be resolved. This DNS data will then be explicitly Reynolds averaged LES filtered. This will allow us to assess the performances of existing models against the corresponding quantities extracted from DNS data. Based on this a priori DNS analysis, we will suggest modifications to the existing models and propose new models if necessary.
The research will be of interest to those involved with designing new generation internal combustion engines and gas turbine combustors. This includes global companies such as Siemens and Rolls Royce. We will keep interested industrial parties informed during the course of this project. We will invite them to attend the progress review meetings. We will also publish project outcomes in reputed journals (eg Combustion and Flame, Physics of Fluids, Proceedings of the Combustion Institute) and conference proceedings (eg International Symposium on Combustion, European Combustion Meeting).
This work is fundamental. We expect that internationally reputed journals will publish project outcomes. The student will work with combustion groups at the University of Cambridge, as well as reputed combustion researchers in the USA, France and Germany.
You will be eligible for this project if you:
- have a 1st class or 2:1 degree in Aerospace, Mechanical and Chemical Engineering, Applied Mathematics, or Applied Physics
- are interested in general area of turbulent combustion
- Contact Prof Nilanjan Chakraborty
Dr Prodip Das
Prodip Das is a Lecturer in Mechanical Engineering. He joined Newcastle University in 2013. He has previously worked for the Lawrence Berkeley National Laboratory in the USA, the University of Waterloo and the National Research Council in Canada, and the Bangladesh University of Engineering and Technology (BUET).
Prodip’s primary research interests span the broad area of energy conversion and storage. He has a particular focus on:
- thermo-fluid aspects of Li-ion batteries
- fuel cells
- flow batteries
- solar-fuel generators
- design and optimisation via additive manufacturing and multi-physics modelling
He is also interested in nature-inspired thermal transport and convective heat transfer.
Defects detection in fuel-cell MEAs using infrared thermography
Fuel cell and fuel-cell-battery hybrid systems are becoming more prominent. We need new manufacturing methods so that the industry can increase production. These methods must provide high quality and lower costs.
This industrial growth will need more accurate information during the manufacturing process. In particular, we need to predict defects in membrane-electrode-assembly (MEA) components.
Defects in MEA components differ in type and extent, depending on the fabrication process. Their effects also differ. These differences depend on the size and location in the cell relative to the reactant flow-field. Cell operating conditions and the component containing the defect also influence the effects. Modern high-volume continuous manufacturing methods need accurate diagnostic systems. The systems must provide high data acquisition and processing rates. We need a deep understanding of the effects of these different kinds of defects to develop such systems. Predictive capabilities for manufacturers are critical for the development of tolerances. Manufacturers also need to be able to assess the effects of material and process changes.
Infrared (IR) thermography can detect defects in fuel cell MEA components. It can also quantify variations in platinum-containing catalyst layer thickness. Thus, it has shown great promise for quality assessment. We have developed a reactive-flow-through (RFT) technique and a DC electronic excitation method.
In the RFT technique, a dilute non-flammable H2/O2 gas-mixture flows through the gas-diffusion electrode. The reaction occurs at the Pt-catalytic sites in the catalyst layer and produces heat.
In the DC excitation method, we apply a DC voltage across a catalyst layer and measure the thermal responses using IR thermography.
These techniques are rapid, non-contact, non-destructive, and suitable for the manufacturing environment. Both methods involve designing non-destructive experiments and developing diagnostic tools and sensors. Both methods will enable engineers to detect and quantify mechanical defects.
In this project, we will use our expertise to develop high-fidelity modelling tools using IR thermography. These tools will play an important role in designing and guiding our experiments. They will enable us to find detection criteria. They will provide guidance for the scale-up of the system. The full-scale system will assist in manufacturing fuel cell components and other clean energy technology materials.
Effective transport properties in complex multi-phase and porous media for clean energy applications
Complex multi-phase and porous media play an important role in many clean energy systems. These include fuel cells, redox flow batteries, Li-ion batteries, and solar fuel generators. Multi-phase porous media are often sandwiched together in these systems. They must allow ingress of the reactant gasses and egress of the product (either liquid or gas).
Describing the multi-phase transport aspects of these materials is particularly challenging. There are mathematical models for these materials. But they rely on accurate estimation of the effective physicochemical properties, including:
- effective gas-phase diffusivities
- absolute and relative permeabilities
- water-droplet adhesion force
- capillary properties
- thermal and electrical conductivities
These properties enhance our understanding of phenomena within the porous transport media. But the assembly of fuel cells and flow batteries is complex. There is a lack of technological advancement for in-situ measurement.
This project will develop a combined experimental-numerical approach. It will use the approach to measure effective properties in complex geometries. We will investigate geometries relevant to electrochemical and solar thermal systems. These include porous transport layers, insulators, radiant absorbers, heat exchangers, and catalyst carriers.
We will also use X-ray tomography and small-angle X-ray scattering. These methods will allow us to characterise complex multi-phase and porous media. This will enable us to measure morphological properties. Properties include porosity, specific surface area, and pore-size distribution.
We will use morphological data to simulate transport processes. Thus, we will be able to determine effective in-situ transport properties.
Multi-scale modelling of polymer-electrolyte fuel cells
There is a global initiative toward a sustainable energy future. Fuel cells are one of the most promising clean energy-conversion technologies. We can use them in both automotive and stationary applications. Polymer-electrolyte fuel cells (PEFCs) receive the most attention. They have higher electrical efficiency, power density, and durability.
PEFCs have shown promising performance improvements in efficiency and durability. But they are not commercially viable. To achieve the robustness needed to operate in many different conditions, they are more costly than current power sources. The processes of fuel cell operation are complex. We could improve PEFCs with a greater understanding of these processes.
Fundamental modelling will provide us with a deep understanding of a PEFC. We will base this on physical models developed from experimental observations. We have used modelling and simulation at the continuum level for years. We use it to help interpret and guide experimental investigations. We also use it to improve and optimise the design and operation of PEFCs. But most of the models are either cell-level or stack-level. There is a lack of connection between multiple scales.
This project will investigate multi-scale models of proton-exchange-membrane fuel cells (PEMFCs) or anion-exchange-membrane fuel cells (AEMFCs).
We will use commercial CFD (computational fluid dynamic) software packages. COMSOL or ANSYS Fluent has inherent advantages over open-source CFD software packages. We will use the model to investigate transport phenomena inside the porous media of PEMFCs and AEMFCs. This will lead to improved performance and design for automotive applications. Thus, it will increase the commercialisation of PEFCs.
Nature inspired thermal design and optimisation using nanofluids
Many engineering applications use convective heat transfer inside cavities. Solar collectors, electronic cooling, lubrication technologies, food processing, and nuclear reactors all use the technology. The cavities can take many forms, including triangular, trapezoidal, cylindrical, square, and wavy. They may also use fins in a variety of shapes. Fins are surfaces extending from the cavity. They increase the rate of heat transfer.
The technology has been extensively analysed for thermal enhancement and optimisation. Modern electronic devices are becoming smaller and smaller. Miniaturisation means that enhancing or optimising heat transfer inside cavities is becoming challenging. We may be able to overcome this challenge by adding different types of fin and filling the cavity with nanofluids. These are a combination of a fluid base and nanoparticles.
We have been investigating the convective heat transfer of nanofluids in cavities. We have employed theoretical and computational modelling, using the constructal design concept. This is based on the constructal law. Adrian Bejan formulated this law in the mid-1990s. The law states:
“For a finite-size system to persist in time (to live), it must evolve in such a way that it provides easier access to the imposed currents that flow through it”.
The generation and evolution of design is a universal phenomenon. It includes configuration, shape, structure, pattern, and rhythm. Hence, it provides a better pathway for thermal design and optimisation in engineering problems. For example, we can achieve a higher heat transfer from a fin by modifying the fin’s aspect ratio, keeping the area ratio (cavity to fin area) constant. As shown in the figure, for Al2O3/water nanofluid, the average Nusselt number (Nuavg) is 24.5 for the optimum shape at Re = 1000. This is nearly 32% and 110% higher than the lowest and highest aspect ratios of the fin (H1/L1 = 0.1 and H1/L1 = 10) respectively.
In this project, we will develop computer models using various cavity geometries and fin shapes. This will provide a better thermal design.
Physics-based thermal degradation modelling of lithium-ion batteries
Around the world, the use of lithium-ion batteries (LiBs) has grown exponentially, and so has research into them. But these volatile high energy storage devices face many problems. Thermal-runaway, goldilocks-effect (cold and hot sensitivity), high cost, short life spans, calendar ageing, and difficulty to transport are just a few of the problems.
We can solve some of these issues using physics-based LiB models. Modelling and simulations are necessary tools. They provide accelerated understanding. This leads to design optimisation. It improves our design of automatic control of batteries and battery systems. We are able to analyse an almost unlimited number of design parameters and operating conditions at a relatively small cost. Experimental observations serve as necessary verification and validation of our models.
There has been a lot of progress in modelling and design optimisation of lithium-ion batteries. Much of the research maps the trade-off between power and energy density. But most studies only use a few design variables. Thus, they limit the optimisation to a narrow range of operating conditions. They do not consider thermal degradation.
This project will develop a physics-based local thermal degradation model of LiB cell using COMSOL. We will then use the model to investigate the first life degradation and second life behaviour of a lithium-ion battery.
Dr Immanuvel Paul
Dr Immanuvel Paul joined as a Lecturer in Thermal Engineering at Newcastle University in October 2020. Before joining Newcastle, he was a postdoctoral research associate at the Center for Turbulence Research, Stanford University, USA. His postdoctoral work, which was funded by the department of energy (DoE) USA, mainly focused on developing numerical models to simulate a novel particle-based volumetric solar receiver.
Mixing enhancement due to bubble induced turbulence
Industrial mixers play a vital role in diverse industries ranging from pharmaceutical, water to petroleum industries. In much of these applications, industrial mixers depend on turbulence for mixing efficiency. Multiscale turbulence has shown to increase the efficiency of mixing through a space-scale unfolding (SSU) mechanism. However, it is not always straightforward to incorporate a multiscale grid in some applications and the resulting pressure-drop due to using grids cannot be avoided.
Recent research from my research group has shown that the characteristics of multiscale turbulence can also be observed in bubble induced turbulence (BIT). However, the mixing aspects of BIT are not yet explored. The outcome of this research would help in designing better industrial mixers.
Mathematical modelling of smart architecture
Climate change is increasingly becoming a huge challenge to tackle. Almost 81% of the energy resources that we currently rely upon come from non-renewable energy resources like fossil fuel. We can approach the climate change challenge in two ways. One is to switch to renewable energy resources. The other one is through efficiently using energy. This project deals with the later aspect through helping construct energy-efficient buildings.
The enormous amount of surface area covered by the building material offers plenty of opportunities to make a building energy efficient. We take up the surfaces like windows, facades and roofs and we make them energy efficient using Nano phase-change glazing materials to increase the overall thermal coefficient and optical properties of these surfaces. The experiments concerning these surfaces are often expensive and time-consuming. Mathematical modelling of smart architecture, which involves all the modes of heat transfer, can be of immense help for the construction industries. We first mathematically model all the processes involved in smart architecture and then solve the governing equations using efficient algorithms including ray-tracing techniques.
Study of multiscale non-equilibrium passive scalar turbulence
Although recent research has illustrated the potential applications of multiscale non-equilibrium scalar turbulence in mixing, much of the fundamental aspects of it are still unknown. These aspects play a major role in developing models for multiscale non-equilibrium turbulence. Without a proper model, it is next to impossible to reap the benefits of non-equilibrium scalar turbulence for mixing industries completely as optimization and uncertainty quantification studies require a proper turbulence model to generate a large dataset.
This project aims to explore the fundamental aspects of the passive scalar turbulence generated by fractal grids. The objective is to provide all the details needed for developing a turbulence model. We have high-fidelity in-house solvers to perform a direct numerical simulation of scalar turbulence. We will consider shear-free and shear scalar turbulence.
Nano non-Newtonian fluids for turbulent heat transfer applications
We live in a world where energy demand increases exponentially day by day. To protect our environment and thus leaving a better world for the next generations, we need clean energy resources and the energy should be used efficiently. The heat transfer fluid (HTF) can play a role in energy production and efficient energy management. For instance, it is a source of energy transport in concentrated solar power plants. In applications such as heat exchangers, cooling of electronic components, automobile radiators and nuclear reactors, the nature of HTF determines how we manage energy efficiently. Therefore, increasing the efficiency of HTF has a plethora of applications related to clean energy.
One of the ways to increase the heat transfer efficiency of the working fluid is to add particles to it. The addition of particles increases the thermal conductivity of the HTF and also increases the mixing efficiency of the HTF. Besides this conventional approach, recent research shows that non-Newtonian fluids act as a better heat transfer fluid with higher efficiency. Besides, non-Newtonian fluids play a major role in many industries including chemical processing, lubrication, hot rolling, and biomechanics industries. In this study, we want to understand the effect of particle suspensions in non-Newtonian fluids.
In the applications mentioned before, heat transfer is due to all modes of heat transfer. Therefore, we analyse a non-Newtonian Nano-fluid to increase its efficiency as an HTF.
Turbulence modelling of non-equilibrium turbulence
More than a decade of research on multiscale non-equilibrium turbulence has shown its potential in diverse applications ranging from reducing the noise of an aircraft to increasing the mixing efficiency in industrial mixers. To translate this research into industrial applications, we need models for non-equilibrium turbulence as the industry cannot afford direct numerical simulation.
The main reason why the existing models fail to simulate non-equilibrium turbulence is because of its peculiar characteristics, particularly with the dissipation rate of turbulent kinetic energy. We will develop new RANS and LES models by incorporating the non-constant dissipation rate into our turbulence modelling theory.
Design of latent heat thermal energy storage systems
Approximately 30% of the total electricity that the United Kingdom (UK) generated in 2017 was from renewable energy resources. While the electricity demand is constant all around the year, the supply of power from renewable energy resources is intermittent due to uneven seasonal and weather variations. Therefore, we address the question ’how can we efficiently store thermal energy?’ in this project.
We focus on latent heat TES. We aim to take the Nano molten salt technology further by using Nano-particles as the filler material in the TES system. The additional modelling challenge here is the way the filler material should be modelled. We propose to develop this filler material model equivalent to porous medium which can then be incorporated into our main flow and heat transfer model. The analysis here will be on the stability of the thermocline due to transient operation of the system, and to understand the parameters that govern the discharge efficiency of the storage tank. This research will help us to design efficient storage tanks.
Drag reduction due to heating of surfaces
As technologies advance, the necessity for high-performance highly-efficient drones with a multitude of capabilities has increased for both civilian and military applications. One of the ways to increase the aerodynamic efficiency of the drones is to increase the ratio of lift to drag coefficient.
In this project, we utilise a bio-inspired technology to improve the L/D ratio. We heat the wings in a fractal manner to see the effect of drag and lift at low pitch angles. Due to the large Reynolds number flows experienced by such aerial vehicles turbulence modelling and understanding is crucial to simulating this phenomenon correctly. Therefore, we simulate partially heated wings in the turbulent flow regime.
Previous projects
Here are the titles of some of the projects that our students have previously undertaken.
- Dr Umair Ahmed:
- Assessment of turbulence models in complex geometries
- Dr Andy Aspen:
- Come fly with me: cost of aviation
- Analysing geothermal heat pumps
- Waste heat recovery from an industrial furnace
- Prof Nilanjan Chakraborty
- Dissipation rate of turbulent kinetic energy transport in premixed flames
- Entropy generation in turbulent premixed flames
- Natural convection of power-law fluids in square enclosures with differentially heated horizontal walls subjected to constant wall temperatures
- Natural convection of power-law fluids in square enclosures with differentially heated horizontal walls subjected to constant wall heat flux
- Natural convection of Bingham fluids in annular spaces with differentially heated vertical walls subjected to constant wall temperatures
- Natural convection of Bingham fluids in annular spaces with differentially heated vertical walls subjected to constant wall heat flux
- Computational modelling of liquid cold plates for electronic cooling
- Effects of inclination on natural convection of Bingham fluids in rectangular enclosures
- Dr Prodip Das
- Effect of surface roughness on heat transfer and entropy generation of mixed convection in nanofluid
- Constructal design of a rectangular fin in a mixed convective confined environment
- Mixed convection of CuO-water nanofluid in a square enclosure with an intruded rectangular fin
- Heat transfer and entropy generation of mixed convection in nanofluid inside a rough cavity
- Mixed convection of nanofluids in a lid-driven rough cavity
- Natural convection of AL2O3-water nanofluid in a wavy enclosure
- Mixed convection flow of nanofluid in a square enclosure with an intruded rectangular fin
- Dr Richard Whalley
- Pumping with no moving parts: innovative low-voltage micro-pumps
- Mixing at the micro-scale: creating turbulence in micro-flows
- Non-Newtonian fluid mechanics: on the testing of an extensional rheometer
- Designing and building a Pelton Wheel
- Real-time analysis with Arduino
Teaching
Taught Programmes
From day one, our Mechanical Engineering Undergraduate Programmes give students a path to become a professional engineer addressing major global challenges.
Our Postgraduate Taught (MSc) Programmes equip students with the advanced skills and expertise to help shape the world.